✕ 閉じる
ものづくり
2022年08月26日
完成までの工程は200以上!福井に眼鏡産業を興した老舗に見る「もの作りの真髄」
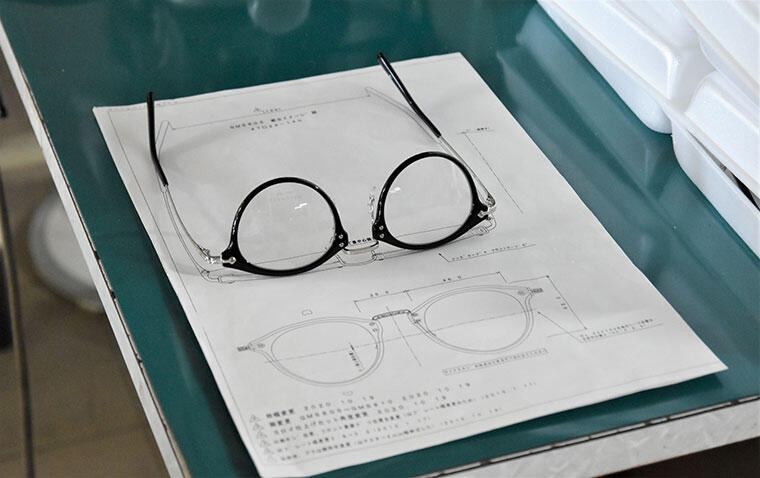
日本有数の地場産業として広くしられるようになった、福井県鯖江市の眼鏡。国内における眼鏡枠の出荷額において、福井県は9割以上のシェアを誇っている。クオリティの高さも随一で、世界の一流ブランドからも生産の依頼が絶えないほどだ。そのもの作りの現場に迫るべく、福井眼鏡産業の祖である増永眼鏡を訪ねた。
なぜ福井県で眼鏡作りが始まったのか
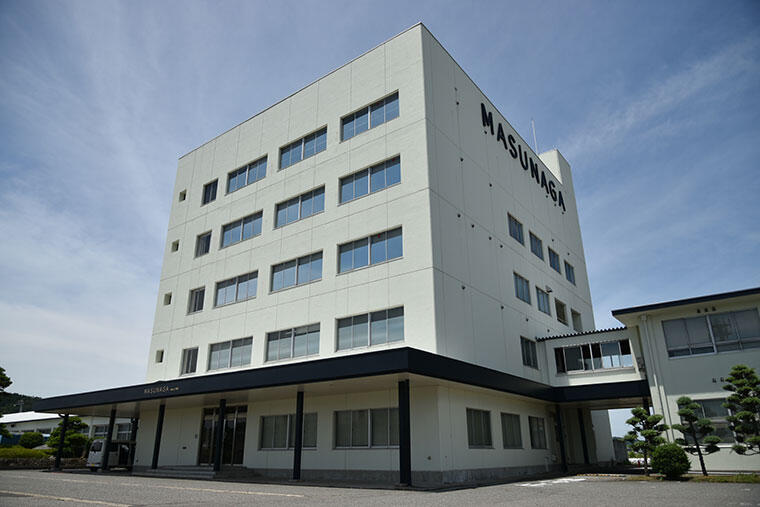
増永眼鏡本社。工場も併設されている。
増永眼鏡が位置するのは、福井県福井市。福井鉄道福武線浅水駅のほど近くだ。
話を伺ったのは、増永眼鏡代表取締役社長の増永宗大郎さん。じつは宗大郎さんの曽祖父にあたる増永五左衛門は増永眼鏡の創業者であると同時に、福井の地にゼロから眼鏡産業を興した人物なのである。
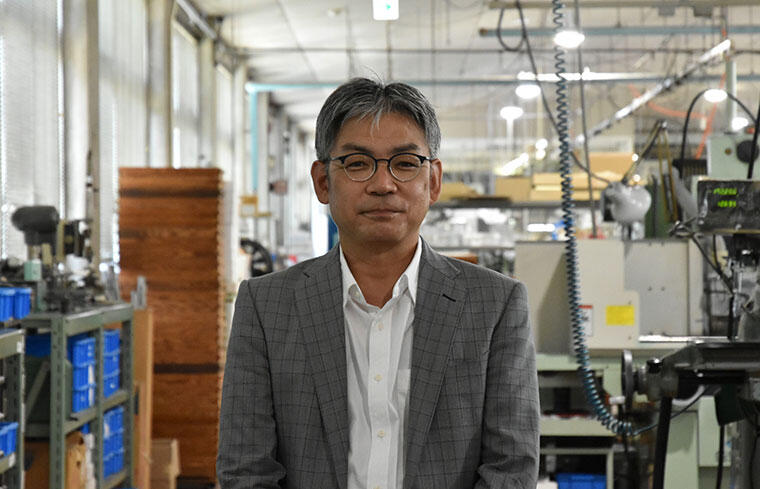
増永眼鏡の5代目社長である増永宗大郎さん。
1898年に村会議員となった増永五左衛門は、雪深い地元の経済を救うため産業を興すことを考えた。そこで、少ない投資で現金収入が得られ、これから需要が高まるであろう眼鏡作りに着目。大阪や東京から職人を招き、1905年に足羽群麻生津村生野(現在の福井県生野町)に工場を設立。これが福井の眼鏡産業の出発点となったのだ。
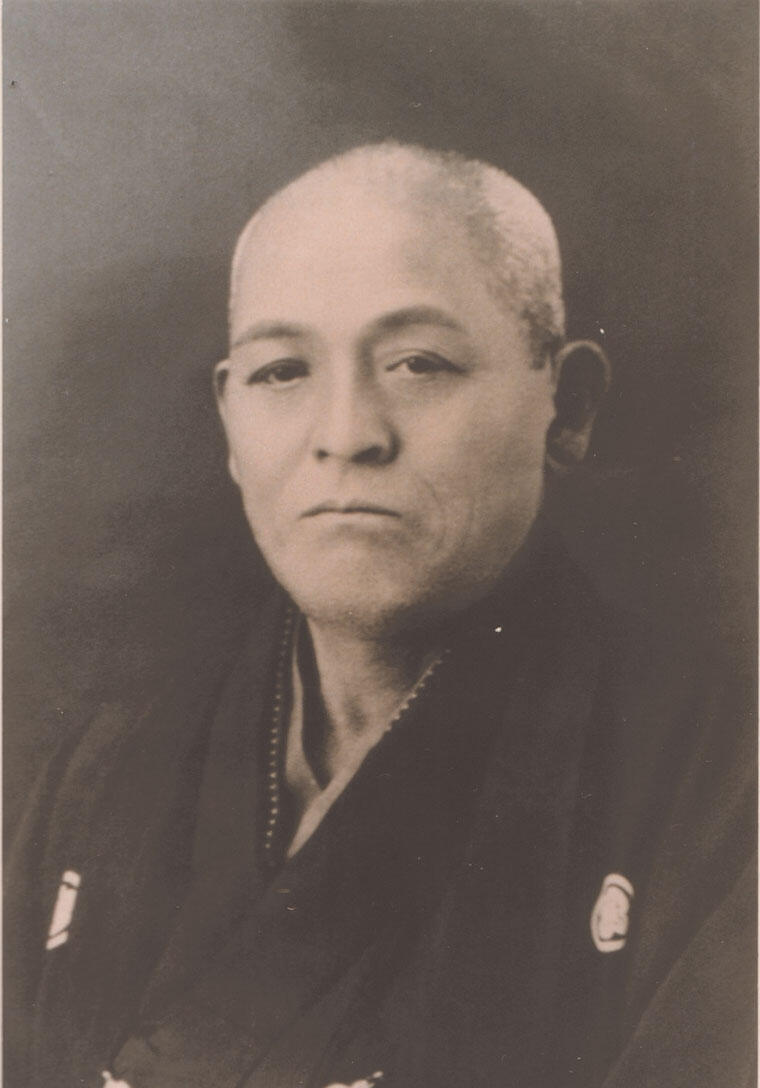
増永五左衛門。眼鏡産業を興すまでの奮闘は、来年公開予定の映画『おしょりん』にも描かれている。
その後、工場で親方や優秀な職人として働いていた鯖江の河和田地区出身者が地元に帰って独立したり、第二次世界大戦後には旧鯖江三十六連隊の広大な跡地の多くが眼鏡工場へと転用されたりしたことで、福井から始まった眼鏡作りは鯖江へと広がり、一大産地となっていったのである。
つねに革新的であり続ける老舗
「会社の歴史が長いこともあり真面目で固い社風と思われがちなんですが、歴史的に見ても当社はドラスティックな事業展開をしてきています。そもそも明治の終わりに、何も素地のないところからいきなり“眼鏡作りを始めよう”という発想が思い切っていますよね(笑)。村のために私財を投じて事業を興そうという発想も、当時はかなり進歩的だったと思います」。
その姿勢は創業以来一貫しており、同社はまだ日本において眼鏡にブランドという概念が浸透していなかった1960年代に自社ブランドを設立。海外への進出も早く、2000年には眼鏡界のアカデミー賞とも称される「Silmo d'or(シルモドール)」にて日本企業として初の金賞を受賞した。2013年、2014年、2015年には3年連続で受賞という快挙も達成している。老舗にして、革新的なデザインでトレンドを牽引する存在でもあるのだ。
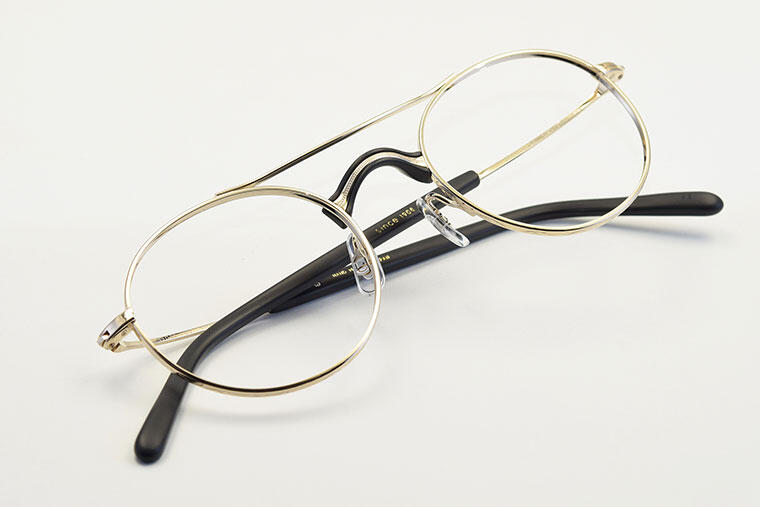
2015年にシルモドールを受賞した「GMS-106」。
それでは、いよいよ眼鏡作りの現場へ。増永眼鏡の工場の特徴は、自社ですべての工程を担う一貫生産であることだ。というのも福井の眼鏡作りは、各工程を専門の工場が担う分業制が主流。眼鏡は小さなアイテムながら完成までの工程数は200以上に及び、一つひとつの専門性が高い。そのため、それぞれの工場が得意分野に集中し、技術に磨きをかけることで産地全体の技術向上を図ってきた。そうしたなか一貫生産にこだわる同社は、稀有な存在なのである。
多くの人の手を介して作られる眼鏡
なにしろ同工場では約300もの工程をこなしているというから、そのすべてを辿るのは難しい。ここでは、いくつかピックアップして紹介しよう。
【プロト製作】
まず最初に通されたのはデザイン室。フレームのデザイン図面が出来上がったら、それをもとに立体的な試作を作ることから眼鏡作りはスタートする。
メタルフレームであれば手作業で金属の板からパーツを切り出し、ロウ付け(溶接)をして、原寸大のプロトタイプを作製。デザインとしての完成度はもちろん、掛けやすさなど眼鏡としての機能性についても十分に検証してから、寸法も入った設計図面へと落とし込まれる。
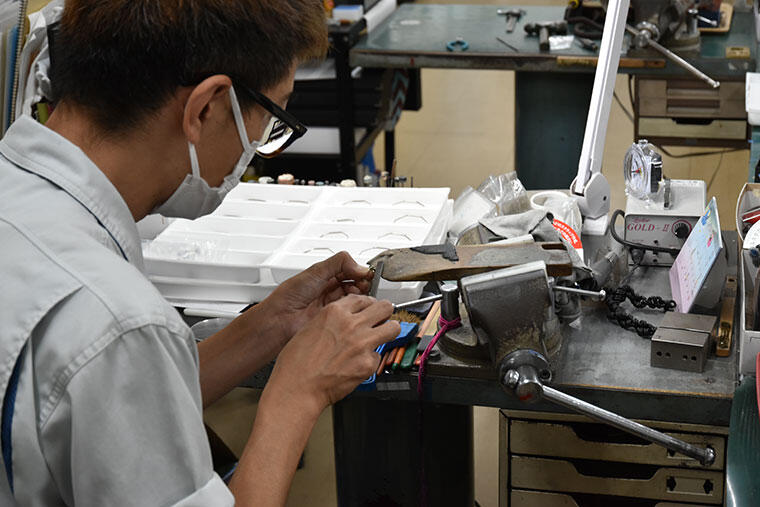
金属の板からパーツを削り出すプロト職人
【プレス】
メタルフレームには、チタン素材を採用。それらはもともとは丸線状や板状であり、専用の金型にセットしてプレス機で数十トンから数百トンもの圧をかけてパーツの形へと成型していく。
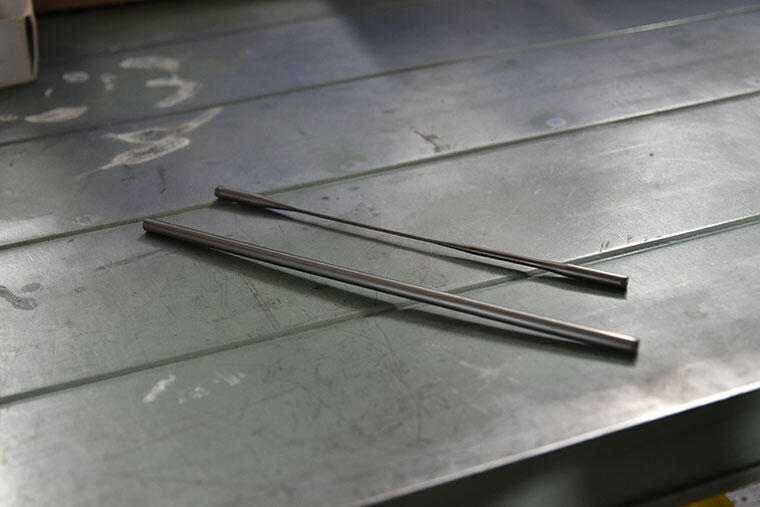
丸線状のチタン。上のものは、スウェージング加工によって中央の径が絞られている。
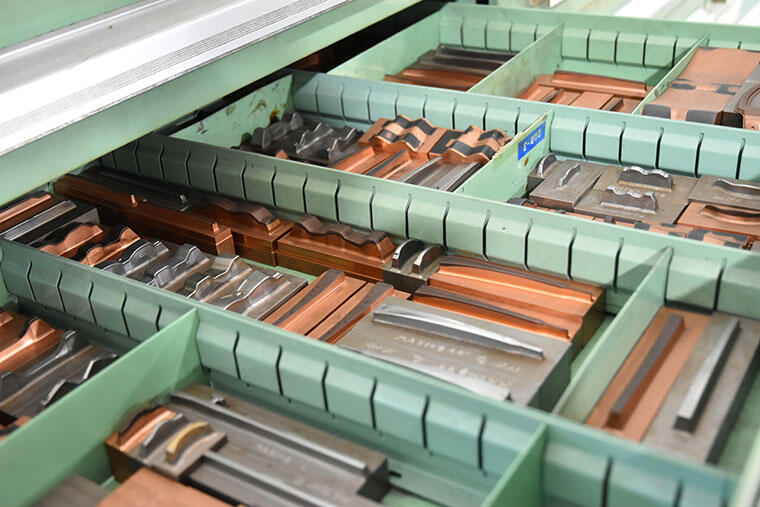
金型を彫るために使用されていた凸型。パーツの形ごとに用意されている。
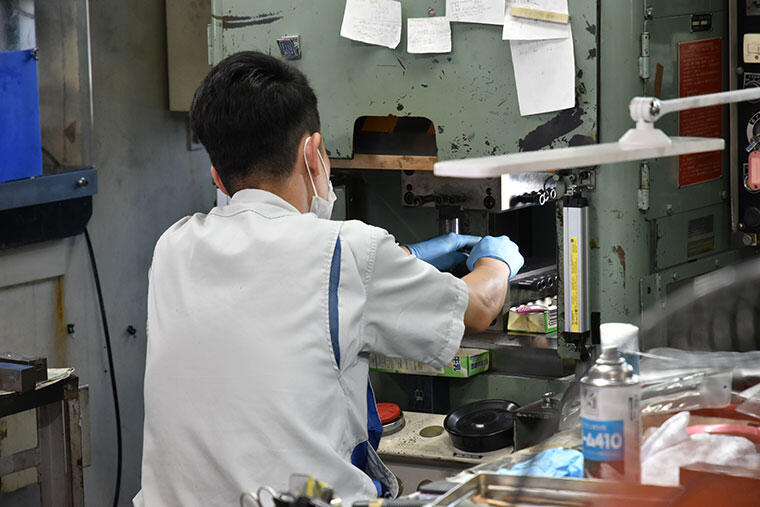
プレス機にパーツを一つずつセットする職人。
チタンは軽量で耐久性が高いため眼鏡に適した素材だが、硬質ゆえに加工が難しい。もちろん1度のプレスだけでは意図する形にならず、様々な種類のプレスを何度も施すことで、ようやくパーツが完成する。
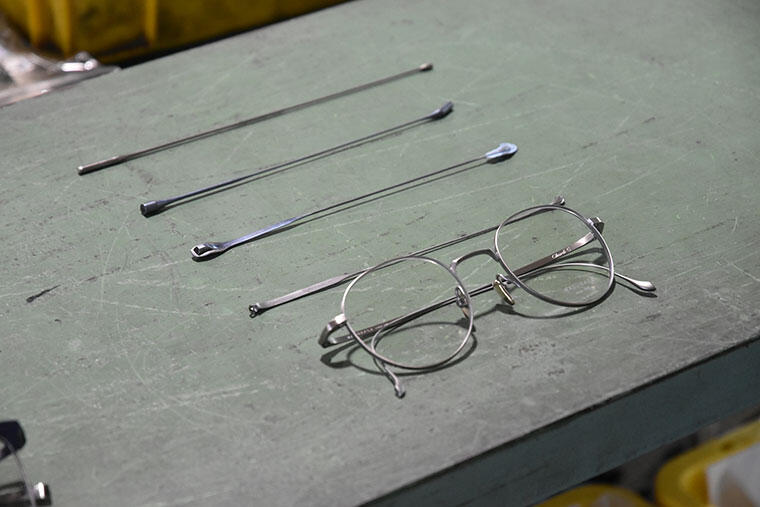
繊細なデザインながら、写真上の細い丸線からテンプル(つる)の形になるまで27工程をも要する。
【生地の切り出し】
プラスチックフレームは、「アセテート」と言われる綿花由来樹脂から作られる。切り出す前はシート状で、その大きさは畳1畳分ほど。レーザー機器を使い、フロントやテンプルなど部位に合わせた大きさに切り出していく。
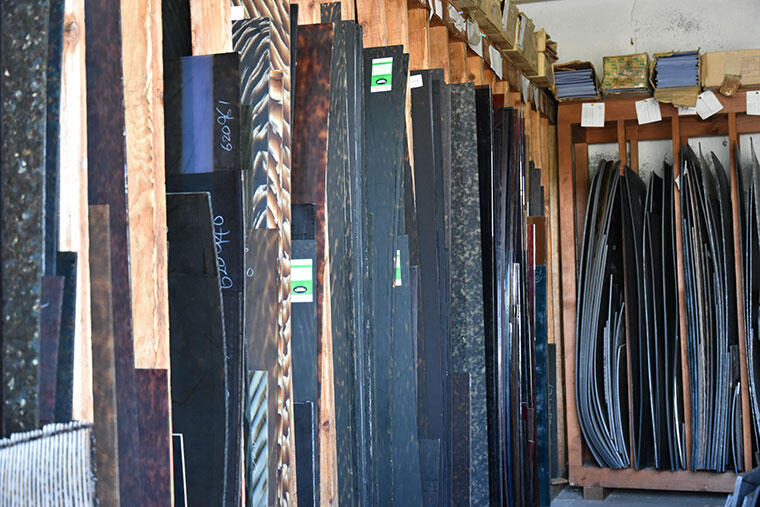
板状のアセテートがズラリ。これらは磨くことで色柄が際立ち艶やかな光沢を放つ。
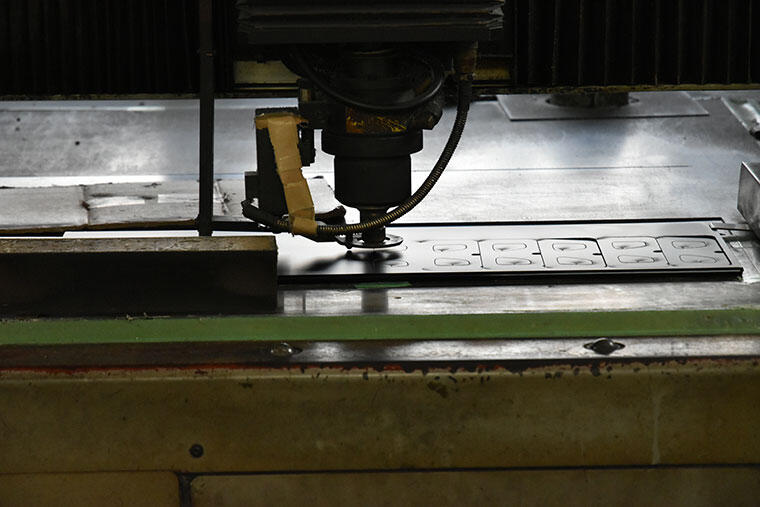
レーザー加工機を使い、生地を精巧に切り出していく。
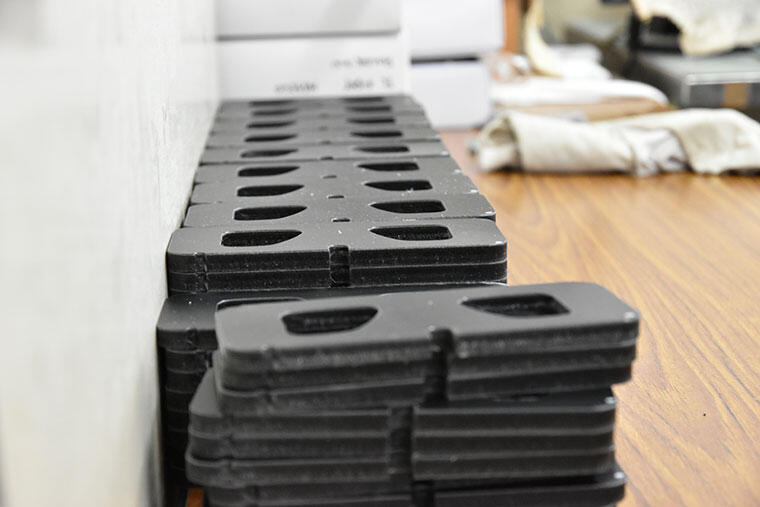
切出されたアセテート生地。
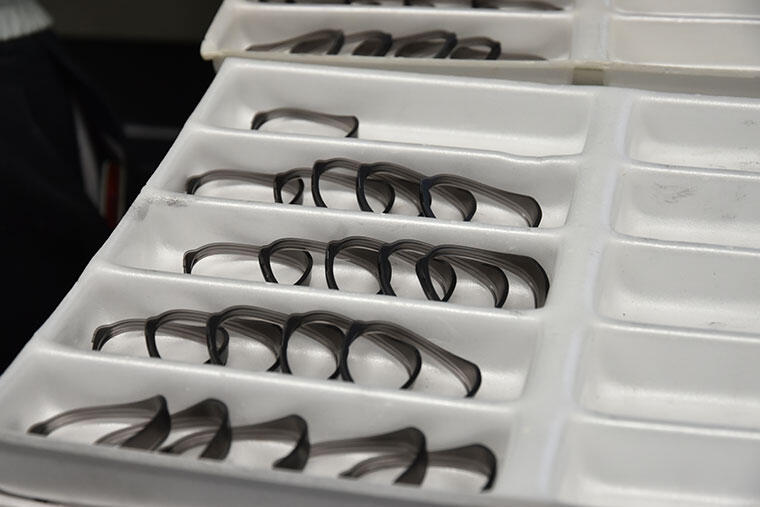
さらに5軸の切削機で立体的に切り出しパーツが完成。こちらはレンズを囲うリムに使用される。
【きさげがけ】
機械を使う工程のみならず、職人による昔ながらの手作業も多く必要とするのが眼鏡作りだ。この「きさげがけ」といわれる工程では、フラットに切り出されたテンプルの表面を小刀のような工具で削り、傷を取りながら面や角を粗めに整えていく。量産品では省かれることもある工程で、このひと手間が仕上がりを大きく左右する。
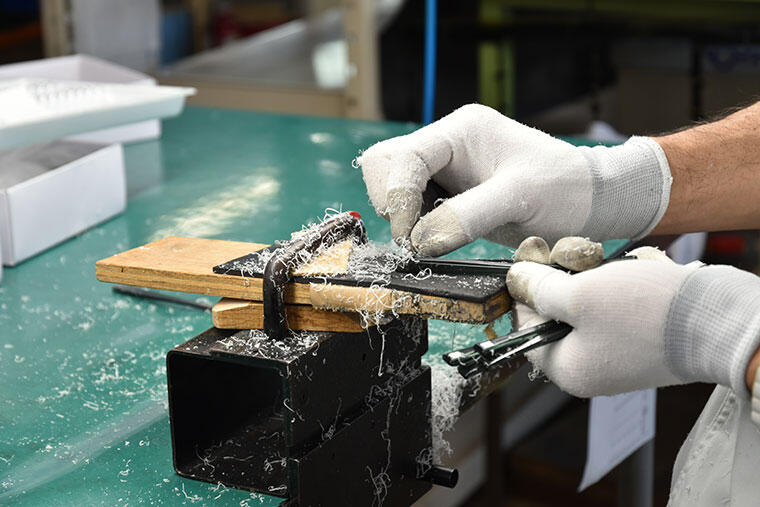
素早く削り出すため、手元はすぐ削りカスでいっぱいに。
【磨き】
フレームの光沢感を出すために欠かせないのが、磨きの工程だ。ここで行なわれているのは、「粗磨き」。綿布でできた円盤状のバフ(羽布)が高速回転しており、この周縁部に泥のような研磨剤を付け、フレームを押し付けるようにして磨く。形を作りながら、表面をきれいに一皮むくようなイメージだ。バフをかける時間や力加減は正確に決まっているわけではなく、職人の経験と勘がものをいう。
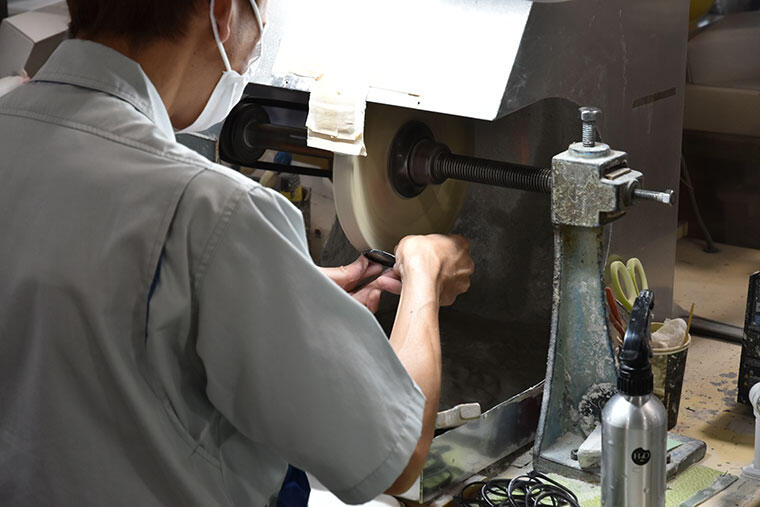
職人が1本ずつ丁寧に磨きをかける。表面が削れ過ぎるとラインが崩れてしまうため、高い技術が求められる。
【ロウ付け】
フロントやテンプルなど各パーツが出来上がったら、それを組み上げるロウ付けの工程へ。細かいパーツとパーツの間にロウ材を付け、熱をかけることで接合していく。レンズを保持する左右のリムに、それらをつなぐブリッジや、テンプルとつながるヨロイなどのパーツがロウ付けされ、眼鏡の形へと近づいていく。
パーツが精巧であっても、ロウ付けに僅かでもズレが生じてしまえば眼鏡全体に歪みが生じてしまう。フレームの安定性や耐久性を左右する重要な工程だ。
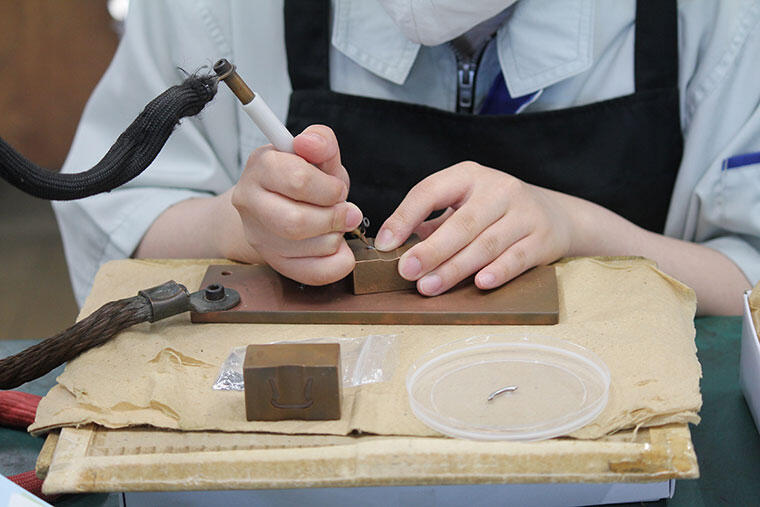
ブリッジの接合部にロウ材を付けているところ。
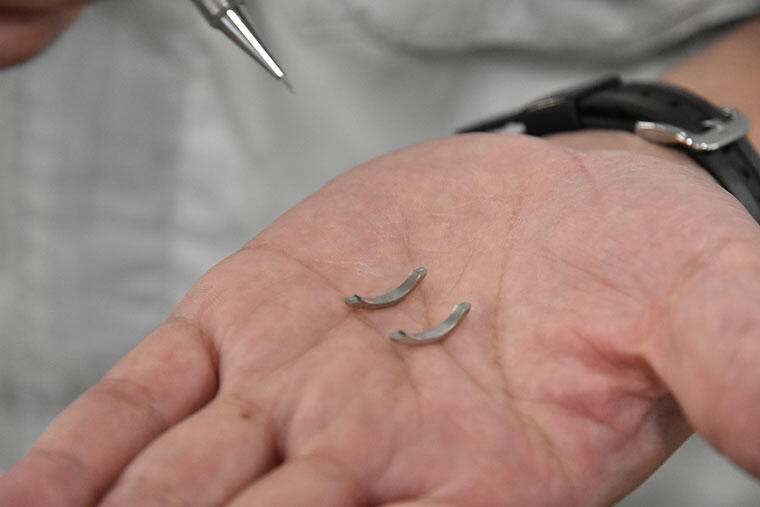
良く見ると上のパーツの接合部(両端)にはロウ材が付けられているのだが、パッと見ではわからないほど細かい。
【ガラ磨き】
組み上がったメタルフレームは、ガラ磨きという工程へ。「ガラ」と呼ばれる八角形のドラムのなかに、研磨剤と眼鏡をセット。ドラムの回転によりフレームの隅々まで研磨剤がかかり、その摩擦によって表面が磨き上げられる。
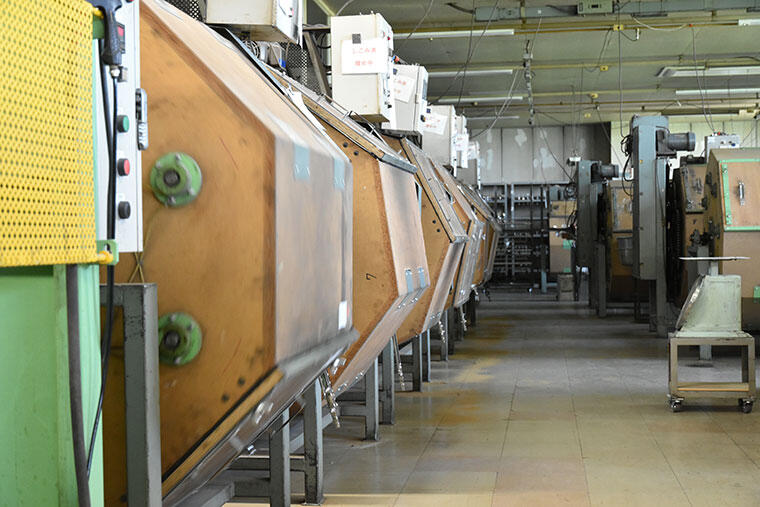
工場では何台ものガラが昼夜問わず回転し続けている。
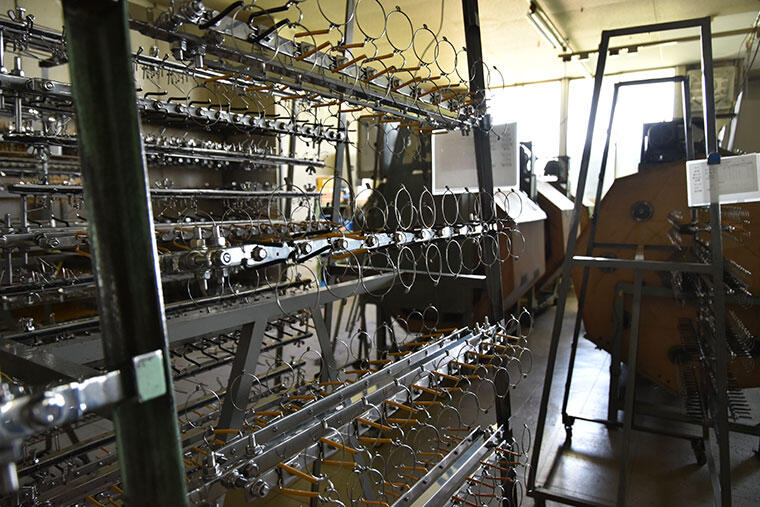
ガラに入れるため、専用のハンガーに掛けられたメタルフレーム。
このガラ磨きは、メタル・プラスチックフレームともに行なわれる工程だが、中に入れる研磨剤の組成や磨く時間、ガラを回す速度は素材やデザインによっても異なる。
増永眼鏡ではこのガラ磨きを3工程に分けており、最初の粗磨きが約8~12時間、次に研磨剤を変えての中磨きが約15時間、さらにまた細かい研磨剤を使っての仕上げ磨きを約15時間行なうという。そう、ほぼ2日間に渡って磨き続けるのだ。同社製品の魅力である上品な艶感は、じっくりと時間をかけたこの工程から生まれているといっても過言ではないだろう。ちなみに、プラスチックフレームは最後にまた職人の手により磨かれるというから驚きだ。
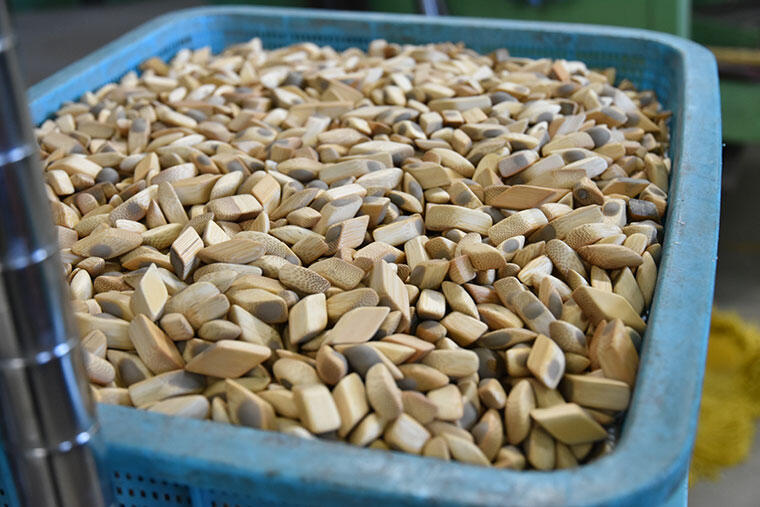
プラスチックフレーム研磨には、研磨剤とともに木製のチップが用いられる。
【表面処理】
一貫生産を行なう同社では、メッキや吹き付け塗装などの表面処理も自社で行なう。
下の写真はイオンプレーティング(IP)を行なっている装置の中の様子。大きな釜のような装置のなかを真空状態にし、金属を加熱蒸発によりイオン化させフレームに金属の皮膜をつけるというもので、フレームにカラーを施すと同時に腐食を防ぐ役目も。
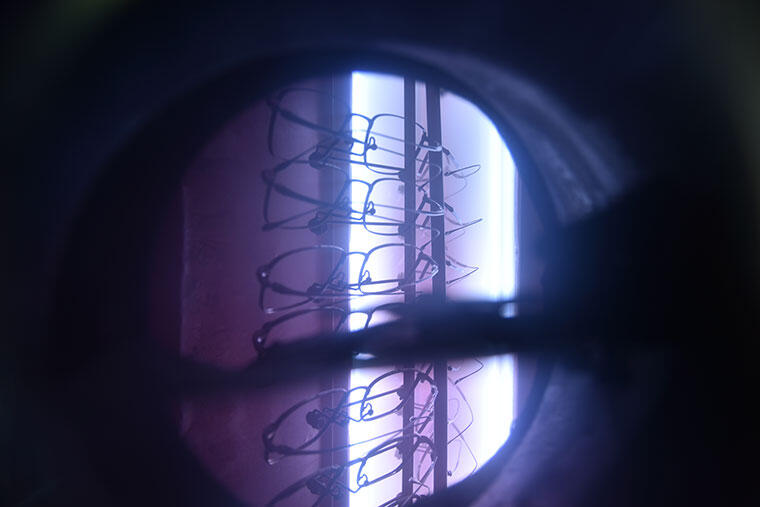
IPは密着強度が高いため剥がれにくく、眼鏡の耐久性も向上する。
ハンガーに掛けられた小さなパーツはネジを受けるワッシャー。正面からは見えない部分のパーツにも、きちんとメッキを施す。こうした丁寧な工程が、全体の質感を高めるのだ。
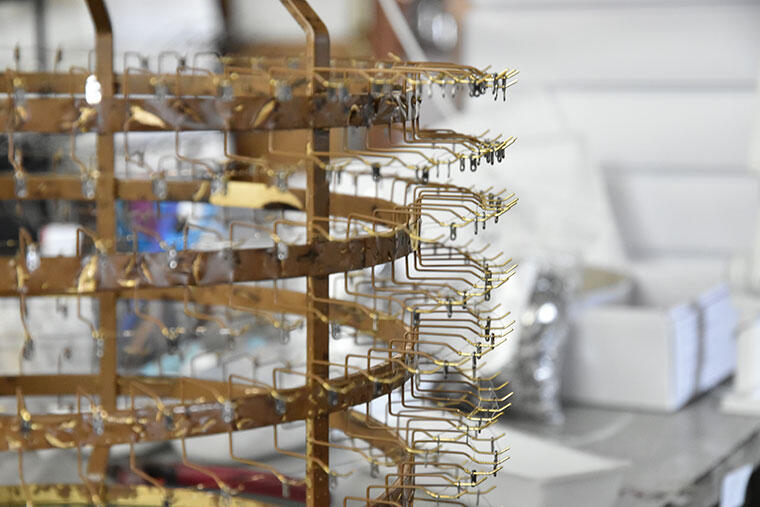
細かなパーツは、専用の治具に一つずつ括りつけられメッキ槽へと浸けられる。
一貫生産により職人の技術を継承する
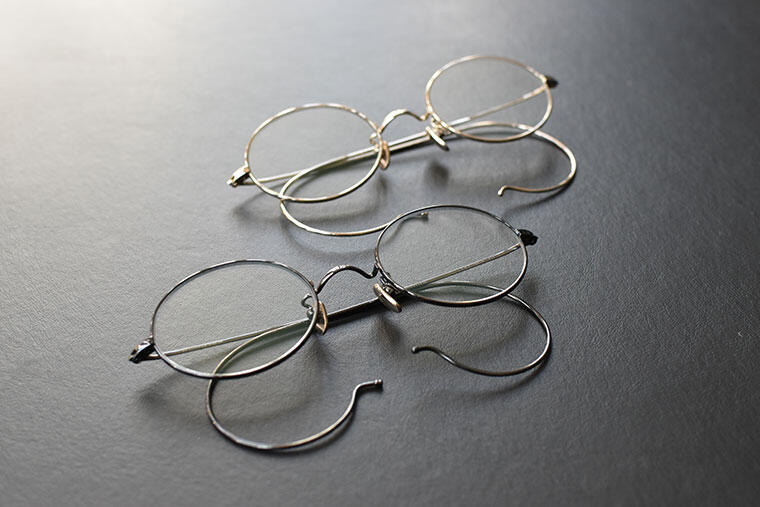
耳に掛かる部分がくるんと丸くなった“縄手テンプル”を採用した「GMS-196TN」。クラシカルなこの意匠を作ることができる職人や工場は、今ではかなり限られている。
さて、これまで紹介した工程は、200以上あるうちの一部に過ぎない。マシンを使うものから昔ながらの手作業を要するものまでとても多様で、手間も掛かっていることがおわかりいただけただろう。
「たしかに企業規模のわりに工程や部門が多いため、工程管理と人材育成には苦労します。ですが、それでも一貫生産にこだわるのは、これまで受け継いできた技術を絶やさないためでもあるんです」
眼鏡づくりの現場においては、生産性を追求するがゆえに次第に採用されなくなった製法も少なくない。職人の高齢化もあいまって、もはや失われかけている技術も出てき始めている。それはもはや、日本の眼鏡作りの伝統が失われつつあることを意味していると言えるだろう。一旦途絶えると、その継承は難しい。そのために増永眼鏡はできる限り社内で一貫生産し、自社で職人を育てることで、技術を継承し続けているのだ。
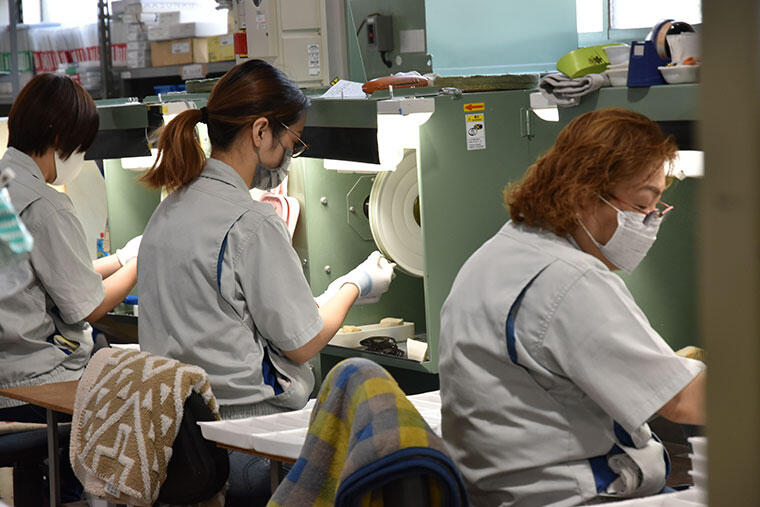
工場では幅広い世代が働いている。
「一つひとつの工程でいえば弊社はナンバーワンでもなければオンリーワンでもなく、専業でやっているところには敵いません。ですが、眼鏡を作るために必要な技術とノウハウはすべて持っているという自負があります。何かあっても全責任を持って対応できるということが、取引先、そして眼鏡を使ってくださるお客様への信頼にもつながっている。そう考えています」。
良い眼鏡の条件、それは“掛け心地”、“耐久性”、“デザイン”の3つがバランス良く融合していること。増永眼鏡が国内外で高く評価される理由は、これらがすべて高次元で融合していることにある。とくに質感の美しさは世界でも随一だ。なぜそれが可能になるのかと聞けば、「どれだけ丁寧に作業をするか、ということですかね」と宗大郎さんはいう。
「『きれいに研磨されたフレームには、それが映えるようきれいな色をつけよう』などと、とにかく前のチームから預かったものを、きちんと次のチームに回していこうという意識が、社員一人ひとりに根付いているんだと思います」
工場取材を続けているとよく耳にするのが、日本の職人は自身が“完璧”とするレベルが、他の国に比べて高いということ。非効率ともいえるほど徹底した丁寧な仕事こそ、メイドインジャパンの真髄であるのだと。
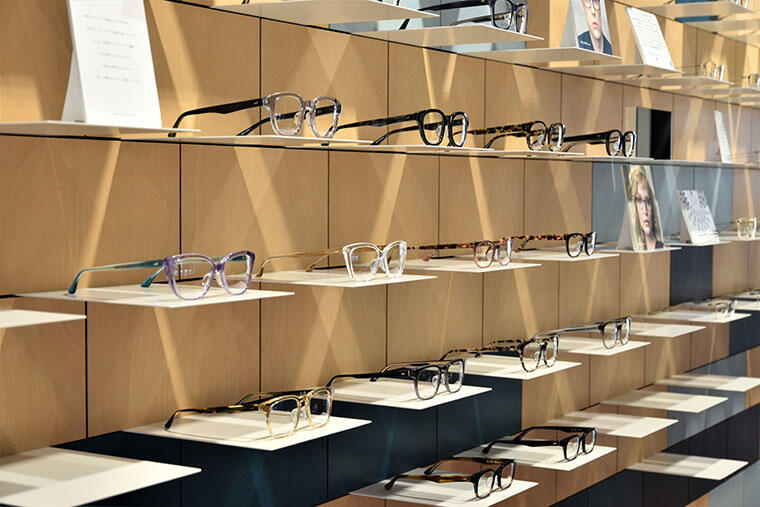
東京・青山にある直営店「MASUNAGA 1905青山店」。ここには増永眼鏡の製品がフルラインナップで揃う。
増永眼鏡には、1世紀以上守り抜いた社是がある。
「当社は、良いめがねをつくるものとする。
出来れば利益を得たいが、やむを得なければ損をしてもよい。
しかし常に良いめがねをつくることを念願する」
革新的なことにもトライしながらも、「良いめがね」を追求するもの作りの本質は揺るがない。増永五左衛門の思いは、今なおしっかりと受け継がれている。
ー了ー
取材協力
増永眼鏡
https://www.masunaga-opt.co.jp/
眼鏡ライター 伊藤美玲
東京都生まれ。出版社勤務を経て、2006年にライターとして独立。眼鏡専門誌『MODE OPTIQUE』をはじめ、『Begin』『monoマガジン』などのモノ雑誌、『文春オンライン』や『Forbes JAPAN 』等のWEB媒体にて、メガネにまつわる記事やコラムを執筆している。『マツコの知らない世界』では“メガネの世 界の案内人”として登場。メガネの国際展示会「iOFT」で行われている「日本メガネ大賞」の審査員も務める。
関連記事
タグ一覧