✕ 閉じる
工業用
2020年04月10日
特別対談:神戸製鋼所 鈴木励一氏×セメダイン 秋本雅人『接合構造物への接着と溶接のハイブリッド接合への期待』(1/4)
自動車車体のマルチマテリアル化にみられるように,さまざまな構造材料の適材適所への適用が広がり,それにともなう接合法についても,鉄—アルミ,高強度鋼—アルミ,金属—樹脂などの接合を対象として,金属間化合物を生成させず,ガルバニック腐食などを起こさず接合できる接着が注目され,その適用範囲も広がってきている。
そこで,本稿では,最近の構造材料への接着剤の適用状況,今後の異種金属材料を用いた構造物への接着剤適用への期待と展望について,溶接界から神戸製鋼所技術開発本部自動車ソリューションセンターマルチマテリアル接合研究室室長の鈴木励一氏と,接着界からセメダイン取締役技術本部長の秋本雅人氏にお話いただいた。
(※産報出版が運営する溶接技術専門誌「溶接技術 2020年4月号」に掲載したコンテンツを、許可を得て転載しています)
異材への各種接合法適用の潮流
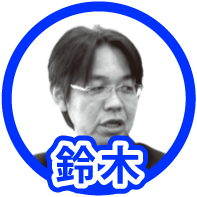
これまで私自身はあらゆる産業の溶接に携わってきており,その中で溶接の歴史について学んできましたし,日本溶接協会の溶接管理技術者資格取得のための研修会の講師も務めてきました。これらの経験を踏まえ,さまざまな接合法がある中で,溶接は太平洋戦争後から本格的に使われてきて,以来,技術が成熟し,事実上最強の接合法であると認識していました。ところが4年ほど前に自動車関係でマルチマテリアル化という流れがでてきました。
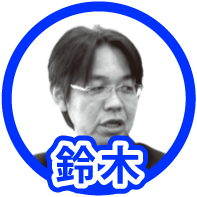
当時は自動車でのアルミ化などはそれ以前からあったものですから今さら何をという感がありました。ところが,欧州での自動車製造の状況をみたとき大きな衝撃を受けました。日本の大学の研究者が研究しているようなサイエンスティックな異材接合,いわゆる溶接をそのまま異材接合に適用するというのではなく,メカニカルな接合と接着剤による接合がふんだんに組み合わされて適用されているのです。日本のようにサイエンスな接合は1つも使われていませんでした。日本ではマルチマテリアル化はこれからだと言われていますが,欧州ではこれからではなく,もう十分に成熟状態にあるということにも驚きました。
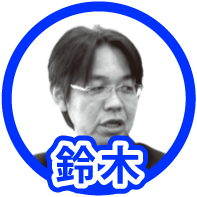
機械的接合も接着も奥が深いもので,今は,それぞれ長所短所はあるにしても溶接に比べ決して侮どれないものだと感じています。溶接でも短所の部分はいくつもあるのですが,私自身はこれまで溶接というのはそういうものなのだと考えて不思議ではありませんでした。しかし,機械的接合や接着の分野から見ると,逆に溶接の短所の部分が露わになって,機械的接合や接着では熱ひずみが起きないとか,異材接合が可能であるとか,スパッタやヒュームが発生せずにクリーンな接合ができるという長所があります。
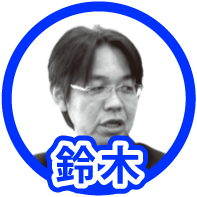
他にも接着に関して言えば,むしろ強度よりもシール性能に優れているという長所があります。自動車のボディでは抵抗スポット溶接による点接合がメインですが,溶接の専門家の中でも自動車ボディでの点接合は,あんなにすき間が空いたような溶接で良いのかと見る向きもありました。抵抗スポット溶接での点接合部のすき間を埋める役割を果たし,しかも振動とか音響を遮蔽することができるのは接着です。溶接ではできない性能を接着では成すことができるわけです。溶接の専門家は自分自身も含めて強度ということにこだわるのですが,もっと大きな観点で接合性能に対して強度以外の機能を取り入れるようにして,あらゆる接合法を組み合わせて自動車をつくっていく。欧州ではすでにそういった観点を取り入れておりますが,日本ではまだ十分ではありません。
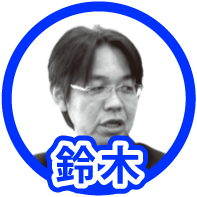
でも,最近ではさまざまなメディアの情報や講演会などを通じて,溶接だけでなくメカニカルな接合や接着というのは実はすごいものなのではないかという認識が生まれてきているように思います。さらに,金属の世界でも自動車で言えばまともに生産できるレベルにおいてハイテン材の高強度化も行き着くところまで来ているように感じるのですが,そうなると,すぐに強度や延性など素材としての基本的性質のパラメータについて議論しがちで,その分,溶接性での議論がおろそかになっています。
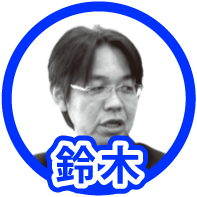
溶接だけに頼れなくなってきたときに,自動車の製造においては溶接の限界ということが顕在化してきているのではないでしょうか。そうなると,他の接合法も世の中には数多く存在していますので,それら各種接合法の長所短所を組み合わせれば,うまくブレークスルーができるのではないかと考えています。
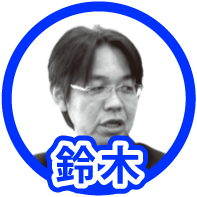
これからは教育的な使いこなしの分野と技術開発という両方に取り組んでいかなければならないでしょうね。そういう意味では,現状では産業界が学術界を追い抜いている状況にあるのではと考えています。とはいえ,接着だけで将来の接合分野はバラ色だとは言えないでしょうし,日本では接着に対し体系的に学べる仕組みも多くは出てきていません。今後は日本の中でも考えて行かねばならないでしょう。
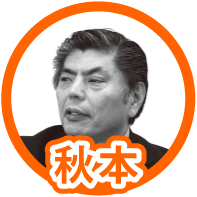
教育ということでは,私は日本接着剤工業会と日本接着学会の両方に身を置いていて,とくに接着剤工業会では初心者向けの講師も務めています(笑)。
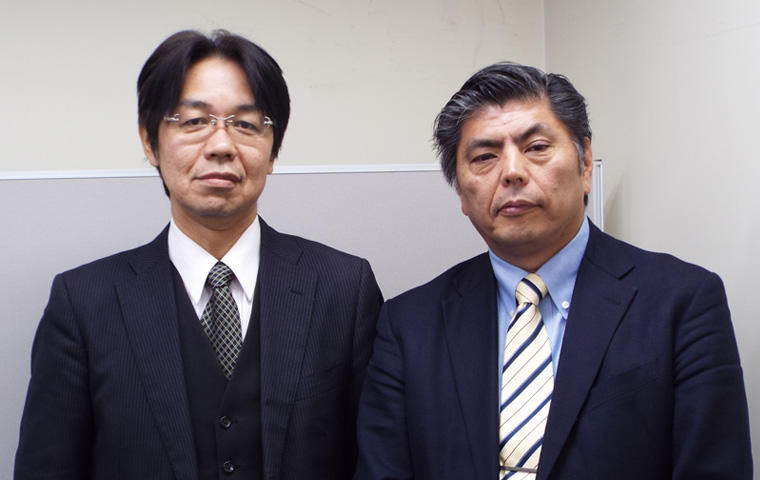
鈴木励一 氏 | 秋本雅人 | |
株式会社神戸製鋼所 | セメダイン株式会社 | |
技術開発本部自動車ソリューションセンターマルチマテリアル接合研究室室長 | 取締役技術本部長 |
※所属・肩書は掲載当時のものです。
接着技術の歴史と現状
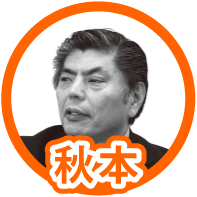
接着というのは歴史を紐解くと6,000年前から存在していました。一方,現在の合成系の接着剤が世の中に登場してきたのはここ100年少し前くらいからです。その適用対象は,集成材とか合板などの構造材からで,その後建築仕上げ材である,床,壁,天井材料の貼り合わせに使われるようになります。あるいは家庭で壊れたモノを修理するのに利用されていました。
その後,1960年代から反応系の接着剤が世の中に登場しました。実は瞬間接着剤の登場は古い方で,アクリル,エポキシ,ウレタン,シリコーンなどの現在構造材に使用されるような接着剤は,西暦2000年頃までに体系化されています。つまり20世紀中には構造材に使用される接着剤はほぼ出揃った訳です。
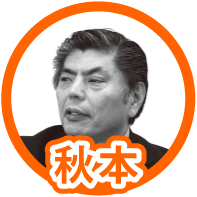
現在,接着剤メーカーでは20世紀の間に体系化されたものを,より機能性を上げるようカスタマイズしています。その中で,日本では5,6年前に自動車を中心とした構造材への接着剤の本格的適用という方向に大きく舵が切られたと考えております。自動車分野では,30年ほど前から接合部の疲労特性を向上させる目的でウエルドボンド工法という溶接と接着のハイブリッド工法が開発され,熱硬化エポキシ樹脂系接着剤が構造用接着剤として使用されてきました。しかし,その後数十年大きな進展はなく,限定的に使用されてきました。接着剤は,疲労特性向上といった役目として期待はされるものの,溶接で耐力は確保しているので,接着はあくまで二次的な抑えという認識であり,車体の強度計算には接着強度は加味しないことが一般的です。
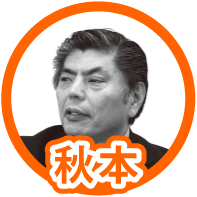
こうした考え方は,自動車に限ったことではなく,建築分野においても,構造物の耐力計算は,溶接やボルト接合の段階ですべて終わっており,接着部が破断しても問題ないような設計にされています。ところが,実際に接着を併用することで,想定以上に大幅に強度が上がる,溶接やボルト接合だけで接合したフレームに比べ,それほど強度的に大きな接着剤を使わなくても接合面に接着剤を併用すると全体の強度が飛躍的に向上するといったことが確認される中で,ここ4,5年で雰囲気が変わってきたように感じています。
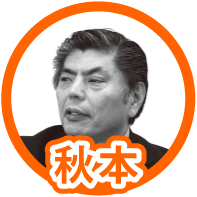
例えば,自動車では,剛性を上げようとか,NVHと言われる快適性向上の1つとしてガタつき防止に接着がとても有効であるということが分かってくる中,軽量化による素材の変化と相まって,使用部位や要求性能にも変化が生まれました。このようなことは欧州で先行していたのですが,実際に構造材料に接着を使用してみたら,明らかに剛性が向上し,ガタつきがなくなる。最近の自動車ではこれから電気自動車が普及するとますます接着が注目されてきていると思います。
(1/4ページ) | 2ページ >> |
関連記事
タグ一覧